Sustainable Battery Manufacturing in Sight: Successful Completion of the BMBF-Funded Project IDcycLIB
After approximately three years, the battery project IDcycLIB, funded by the German Federal Ministry of Education and Research (BMBF) with around 7 million euros, has successfully concluded in December 2024. During the final project meeting at the Fraunhofer Institute for Silicate Research ISC in Würzburg, the outstanding results of the project were presented.
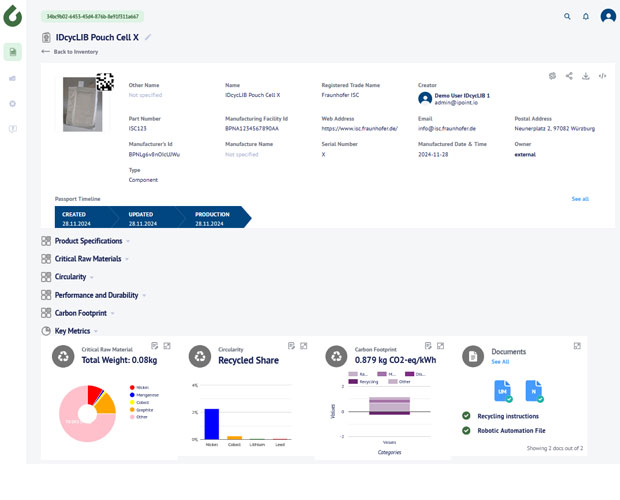
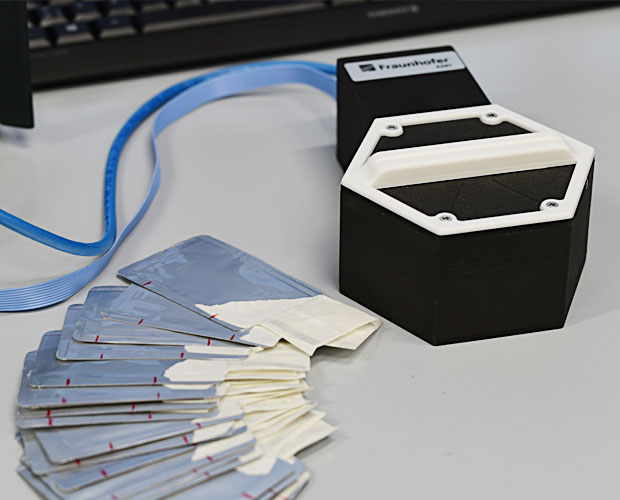
Environmentally Friendly Battery Production
One of the highlights of the project is the transition of cathode production to an aqueous process. This innovation makes battery manufacturing significantly more sustainable. Furthermore, an economic evaluation of the new battery recycling processes was conducted, which are already more cost-effective in pilot scale than the pyrometallurgical and hydrometallurgical processes previously used in the industry. The project team can look back with pride on their collective efforts. All goals and milestones of the project, coordinated by Carl Padberg Zentrifugenbau GmbH, with ten direct project partners and two associated partners, have been achieved. The potential for commercial implementation of the results is high.
Key Developments in the IDcycLIB Project
The collaborative research project IDcycLIB focused on developing a sustainable battery lifecycle with in 2021:
- "Greener Lithium Batteries" using water-based processes in cathode production.
- "Design for Recycling" to facilitate the processing of retired batteries later, e.g., easier separation of sealing seams.
- Detectability / Battery Passport – clear identification through magnetic and fluorescent marker particles.
- Water-based recycling processes – electrohydraulic fragmentation along material boundaries and innovative centrifuge technologies.
- Life Cycle Assessment and Life Cycle Costing – consideration of the entire manufacturing and lifecycle of the battery concerning its environmental impact, including a digital platform for implementing the required battery passport.
Project Coordinator Felix Seiser from Carl Padberg Zentrifugenbau GmbH stated: "This addressed the complete value creation process of the battery and its improvement potentials in terms of environmental friendliness, performance, and economy."

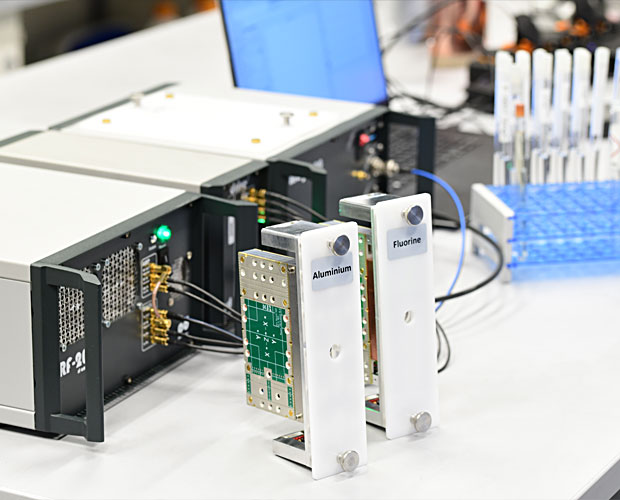
Importance of the Digital Battery Passport
The European Battery Regulation mandates a meaningful labeling for batteries in the future. This labeling provides essential information for the safe operation and efficient recovery of battery materials, including the carbon footprint. However, technical aids and standards for capturing production data and individual assignment to specific battery cells have not yet been uniformly specified.
Dr. Andreas Flegler, scientific coordinator of the project at Fraunhofer ISC, explained: "In the IDcycLIB project, we developed processes and materials that enable automated and individualized data collection in cell production, as well as transfer into an appropriate database system." The core of the work in this area was the definition of a battery passport by iPoint. This allows for the first time to map the entire journey, from cell production, data collection during production, allocation to a UUID, data storage, interfaces, to the identification of the cells, retrieval, and display of the battery passport. Additionally, this is done with a tamper-proof marking that is extremely robust and thus ideal for durable products like batteries. Using specially designed magnetic marker particles from the particle group at Friedrich-Alexander-University Erlangen-Nuremberg, together with the detection methodology from the Fraunhofer Institute for Integrated Circuits IIS and particle patterns from Polysecure, each battery cell can be securely identified with its unique "fingerprint." Even individual components such as electrode materials were labeled with fluorescent marker particles from Polysecure to track the path of materials and facilitate sorting in the recycling process.
Developing this marker system, which can also label individual components inside the battery cell without disrupting function or shortening lifespan, was a special challenge for the project team. The unique identity through the particle patterns was linked with a "Universally Unique Identifier" (UUID). This UUID is a globally unique sequence of numbers used for the precise identification of information in computer systems. The UUID connects the respective cell or component with the corresponding dataset generated during production. This allows for addressing different levels – individual passports for each component as well as for the entire battery – and providing relevant information regarding product characteristics, composition, critical raw materials, recyclability, carbon footprint, and specific metrics.
For retrieving information, a new detection technology from Polysecure was used in the project, which can quickly read and process the information stored in the particle patterns. The provision of production data in the battery passport was made possible using data models from existing data exchange networks like the CATENA-X Automotive Network and in preparation for the "Eclipse Dataspace Connector." The required interoperability – meaning the ability to exchange data across common systems – is thus secured, enabling quick access to the data stored in the battery passport.
Advancements in Electrode Manufacturing – Water-based Processing
For a more sustainable manufacturing of battery components, the production process of the cathodes was scrutinized in IDcycLIB. For the binder material used, PVDF (Polyvinylidene fluoride) – a member of the increasingly criticized PFAS family – the IDcycLIB team at Fraunhofer ISC employed a cellulose-based binder. Additionally, the solvent NMP (N-Methyl-2-Pyrrolidone), previously used in cathode manufacturing, was replaced with water. NMP is considered reproduction toxic, meaning it can impair reproductive ability.
The water-based process developed in IDcycLIB is therefore a significant step toward more environmentally friendly battery manufacturing. "Water is in principle the desired process medium. However, we faced the challenge that the common cathode materials and also the current collectors made of aluminum were damaged by water," said Flegler. To protect the active material required for battery charge on the cathodes from damage, the Fraunhofer ISC team modified the surface with a special coating. The cathode manufacturing process with the more environmentally friendly materials was scaled up to a roll-to-roll process, producing battery cells at prototype scale for subsequent lifecycle tests and recycling. The water-based process is a true novelty at this scale and offers another advantage, as Seiser explains: "Thanks to the water-soluble cellulose binder, we can also revert to water as a solvent during later recycling."
Economic Direct Recycling
As a particular success of the project, partners evaluate the advancements in direct recycling. The battery cells are cleanly separated with a new method, the so-called electrohydraulic defragmentation at project partner REELEMENTS along the material boundaries and can then be separated into individual material fractions, that means "classified", using innovative and automated centrifuge technology from CEPA developed in IDcycLIB. This enables functional recovery of battery materials, which can be used directly for the production of new battery cells.
Aging of the materials can be remedied through regeneration processes. With new measurement technology, the content of lithium, fluorine, and alumina in the process water can also be determined directly and quickly (within minutes). "Direct recycling not only has high ecological potential compared to the state of the art. It is also already more economical, even in our small project scale, than conventional processes such as pyrometallurgy and hydrometallurgy," concludes project coordinator Seiser proudly. This advantage was clearly demonstrated by the lifecycle analysis of project partner EurA. Thus, a significant step forward has truly been achieved in the IDcycLIB project.
Further Information and Publications
»Magnetic Supraparticles as Identifiers in Single-Layer Lithium-Ion Battery Pouch Cells«
S. L. Deuso, S. Ziegler, D. Weber, F. Breuer, D. Haddad, S. Müssig, A. Flegler, G. A. Giffin, K. Mandel, ChemSusChem 2024, e202401142,
»Influence of Phosphate Surface Coating on Performance of Aqueous-Processed NMC811 Cathodes in 3 Ah Lithium-Ion Cells«
Felix Nagler, Nino Christian, Andreas Gronbach, Franziska Stahl, Philip Daubinger, Dr. Andreas Flegler, Dr. Michael Hofmann, Dr. Guinevere A. Giffin
The Partners
- Carl Padberg Zentrifugenbau GmbH (Projektkoordination)
- Fraunhofer-Institut für Silicatforschung ISC
- Fraunhofer-Institut für Integrierte Schaltungen IIS
- Projektgruppe Magnetresonanz- und Röntgenbildgebung (MRB)
- Friedrich-Alexander-Universität Erlangen-Nürnberg
- Polysecure GmbH
- Pure Devices GmbH
- REELEMENTS GmbH
- iPoint-systems GmbH
- EurA AG
- BASF SE (assoziierter Partner)
- Leclanché (assoziierter Partner)
Last modified: