Nachhaltige Batteriefertigung in Sicht: Erfolgreicher Abschluss des BMBF-geförderten Projekts IDcycLIB
Nach rund 3 Jahren Laufzeit ist im Dezember 2024 das vom Bundesministerium für Bildung und Forschung (BMBF) mit rund 7 Mio. Euro geförderte Batterie-Projekt IDcycLIB zum guten Abschluss gelangt. Beim letzten Projektmeeting am Fraunhofer-Institut für Silicatforschung ISC in Würzburg, wurden die herausragenden Ergebnisse des Projekts vorgestellt.
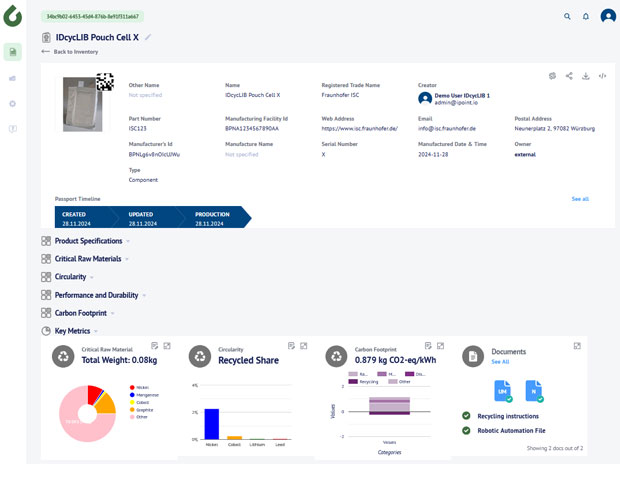
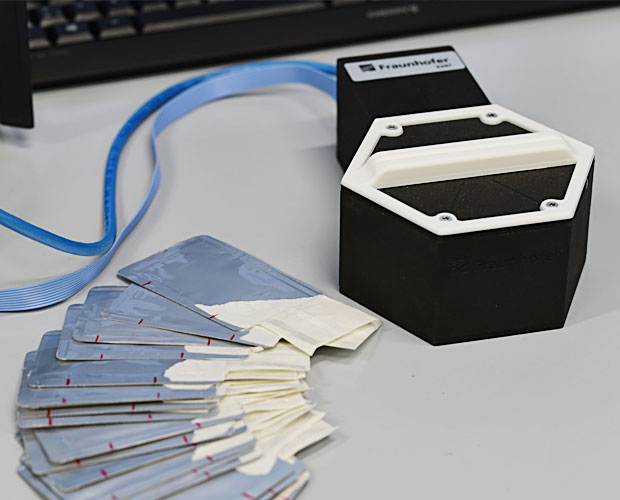
Umweltfreundliche Herstellung von Batterien
Zu den Glanzlichtern des Projekts gehört die Umstellung der Kathodenproduktion auf einen wässrigen Prozess. Diese Neuerung macht die Batteriefertigung deutlich nachhaltiger. Zudem wurde eine ökonomische Bewertung der neuen Batterie-Recyclingverfahren durchgeführt, die bereits im Pilotmaßstab wirtschaftlicher sind, als die bisher in der Industrie genutzten pyrometallurgischen und hydrometallurgischen Verfahren. Das Projektteam kann stolz auf die gemeinsame Arbeit zurückblicken. Alle Ziele und Meilensteine des von der Carl Padberg Zentrifugenbau GmbH koordinierten Projekts mit zehn direkten Projektpartnern und zwei assoziierten Partnern wurden erreicht. Das Potenzial für eine kommerzielle Umsetzung der Ergebnisse ist hoch.
Wichtige Entwicklungen im Projekt IDcycLIB
Das Verbundforschungsprojekt IDcycLIB hatte sich im Jahr 2021 mit fünf zentralen Arbeitszielen auf die Entwicklung eines nachhaltigen Batterie-Lebenszyklus konzentriert:
- »Grünere Lithium Batterien« mit wasserbasierten Prozessen bei der Kathodenherstellung
- »Design for Recycling«, um später das Aufarbeiten von ausgemusterten Batterien zu erleichtern, z. B. leichteres Lösen von Siegelnähten
- Detektierbarkeit / Batteriepass – eindeutige Identifizierung durch magnetische und fluoreszierende Markerpartikel
- Wasserbasierte Recyclingprozesse – elektrohydraulische Zerkleinerung entlang der Materialgrenzen und neuartige Zentrifugentechnologien
- Life Cycle Assessment und Life Cycle Costing – Betrachtung des gesamten Herstellungs- und Lebenszyklus der Batterie hinsichtlich ihrer Auswirkungen auf die Umwelt, eingeschlossen eine digitale Plattform für die Umsetzung des geforderten Batteriepasses
Projektkoordinator Felix Seiser von der Carl Padberg Zentrifugenbau GmbH: »Damit wurde der komplette Wertschöpfungsprozess der Batterie und seine Verbesserungspotenziale hinsichtlich Umweltfreundlichkeit, Leistung und Wirtschaftlichkeit adressiert.«

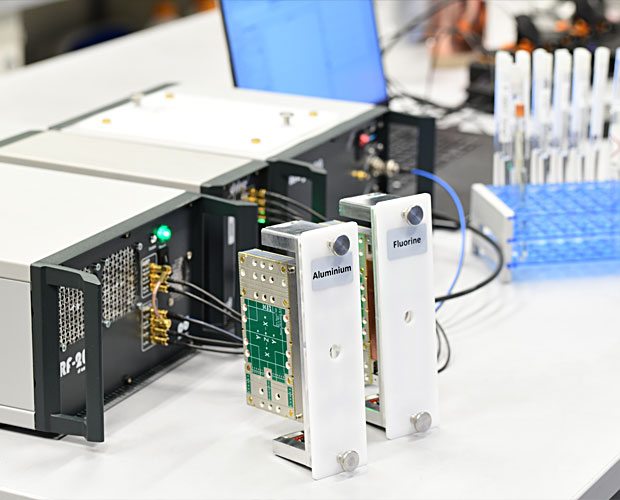
Bedeutung digitaler Batteriepass
Die europäische Battery Regulation schreibt für die Zukunft eine aussagekräftige Kennzeichnung für Batterien vor. Diese Kennzeichnung liefert wichtige Informationen für den sicheren Betrieb und die effiziente Rückgewinnung von Batteriematerialien und beziffert auch den CO2-Fußabdruck. Technische Hilfsmittel und Standards für die Erfassung der Produktionsdaten und individuelle Zuordnung zu einzelnen Batteriezellen sind aber noch nicht einheitlich vorgegeben.
Dr. Andreas Flegler, wissenschaftlicher Koordinator des Projekts am Fraunhofer ISC erläutert: »Im Projekt IDcycLIB haben wir Verfahren und Materialien entwickelt, die eine automatisierte und individualisierte Datenerfassung in der Zellproduktion sowie eine Übertragung in ein geeignetes Datenbanksystem möglich machen.« Kern der Arbeit in diesem Bereich war die Definition eines Batteriepasses durch ipoint. Damit wird es erstmals möglich, den ganzen Weg abzubilden, von der Produktion der Zellen, der Datenerhebung bei der Produktion, der Zuordnung zu einer UUID, der Datenablage, der Schnittstellen bis hin zur Identifikation der Zellen, dem Abruf und der Darstellung des Batteriepasses. Zudem erfolgt dies mit einer fälschungssicheren Markierung, die äußerst robust und somit ideal für langlebige Produkte wie Batterien geeignet ist. Mit speziell designten magnetischen Markerpartikeln der Partikelgruppe an der Friedrich-Alexander-Universität Erlangen-Nürnberg, zusammen mit der Detektionsmethodik vom Fraunhofer-Institut für Integrierte Schaltungen IIS und den Partikelmustern von Polysecure kann jede Batteriezelle fälschungssicher mit ihrem ganz persönlichen »Fingerabdruck« identifiziert werden. Selbst einzelne Komponenten wie Elektrodenmaterialien wurden mit fluoreszierenden Markerpartikeln von Polysecure versehen, um den Weg der Materialien zu verfolgen und das Sortieren im Recyclingprozess zu erleichtern.
Dieses Markersystem zu entwickeln, das auch im Inneren der Batteriezelle einzelne Komponenten kennzeichnen kann, ohne dabei die Funktion zu stören oder die Lebensdauer zu verkürzen, war eine besondere Herausforderung für das Projektteam. Die eindeutige Identität über die Partikelmuster wurde mit einem sogenannten »Universally Unique Identifier« (UUID) verknüpft. Diese UUID ist eine weltweit jeweils nur einmal vorkommenden Ziffernfolge, die zur eindeutigen Identifikation von Informationen in Computersystemen verwendet wird. Die UUID verbindet die jeweilige Zelle bzw. Komponente mit dem zugehörigen, in der Produktion erzeugten Datensatz. Damit können verschiedene Ebenen – individuelle Pässe für die einzelnen Komponenten sowie für die Gesamtbatterie – adressiert werden und die relevanten Informationen über Produkteigenschaften, Zusammensetzung, kritische Rohstoffe, Rezyklierbarkeit, CO2-Fußabdruck und spezifische Messgrößen bereitgestellt werden.
Für das Aufrufen der Informationen wurde im Projekt eine neue Detektionstechnologie von Polysecure eingesetzt, die diese im Partikelmuster gespeicherte Information schnell lesen und verarbeiten kann. Die Bereitstellung der Produktionsdaten im Batteriepass wurde mittels der Datenmodelle bestehender Datenaustausch-Netzwerke wie dem CATENA-X Automotive Network und in Vorbereitung auf den »Eclipse Dataspace Connector« ermöglicht. Die geforderte Interoperabilität – das heißt die Möglichkeit, über gängige Systeme Daten auszutauschen – wird so gesichert und der schnelle Zugriff auf die im Batteriepass gespeicherten Daten ermöglicht.
Fortschritte in der Elektrodenherstellung
Für eine nachhaltigere Herstellung von Batteriekomponenten wurde in IDcycLIB der Herstellprozess der Kathoden unter die Lupe genommen. Für das als Binder-Material eingesetzte PVDF (Polyvinylidenfluorid) – ein Mitglied der zunehmend in die Kritik geratenen PFAS-Familie – setzte das IDcycLIB-Team am Fraunhofer ISC einen Binder auf Cellulosebasis ein. Und das bisher bei der Kathodenherstellung genutzte Lösemittel NMP (N-Methyl-2-Pyrrolidon) wurde durch Wasser ersetzt. NMP gilt als reproduktionstoxisch, das heißt, es kann die Fortpflanzungsfähigkeit beeinträchtigen.
Der in IDcycLIB entwickelte wasserbasierte Prozess ist daher ein großer Schritt hin zu umweltfreundlicherer Batterieherstellung. »Wasser ist natürlich immer das Wunsch-Prozessmittel. Aber hier hatten wir mit der Schwierigkeit zu kämpfen, dass die üblichen Kathodenmaterialien und auch die Stromableiter aus Aluminium durch Wasser geschädigt wurden,“ so Flegler. Um das für die Speicherung der Ladung in der Batterie benötigte Aktivmaterial auf den Kathoden vor Schäden zu schützen, modifizierte das Team des Fraunhofer ISC die Oberfläche mit einer speziellen Beschichtung. Das Kathodenherstellungsverfahren mit den umweltfreundlicheren Materialien wurde auf einen Rolle-zu-Rolle Prozess hochskaliert. Damit wurden Batteriezellen im Prototypenmaßstab für die anschließenden Lebensdauertests und das Recycling produziert. Der wasserbasierte Prozess ist in diesem Maßstab ein echtes Novum und bietet einen weiteren Vorteil, wie Seiser erklärt: »Dank des wasserlöslichen Cellulose-Binders können wir auch beim späteren Recycling auf Wasser als Lösemittel zurückgreifen.“
Wirtschaftliches Direct Recycling
Als besonderen Erfolg des Projekts werten die Partner die Fortschritte im Direct Recycling. Die Batteriezellen werden mit einem neuen Verfahren, der sog. elektrohydraulischen Zerkleinerung (EHZ) bei Projektpartner ReElements entlang der Materialgrenzen sauber aufgespalten und lassen sich dann mit innovativer und in IDcycLIB automatisierten und skalierten Zentrifugentechnologie von CEPA in die einzelnen Materialfraktionen trennen, d. h. »klassieren«. So können die Batteriematerialien funktionserhaltend zurückgewonnen und direkt für die Herstellung neuer Batteriezellen eingesetzt werden.
Eventuelle Alterung der Materialien kann durch Regenerationsverfahren geheilt werden. Mit neuer Messtechnologie wird dabei auch direkt und schnell (innerhalb weniger Minuten) der Gehalt an Lithium, Fluor und Aluminium im Prozesswasser bestimmt. »Das direkte Recycling hat nicht nur hohes ökologisches Potenzial gegenüber dem Stand der Technik. Es ist auch bereits in unserem kleinen Projekt-Maßstab wirtschaftlicher als die herkömmlichen Prozesse wie Pyrometallurgie und Hydrometallurgie«, schließt Projektkoordinator Seiser stolz. Dieser Vorteil wurde durch die Lebenszyklusanalyse des Projektpartners EurA eindeutig nachgewiesen. Damit ist im Projekt IDcycLIB wirklich ein großer Schritt nach vorne gelungen.
Weiterführende Informationen und Publikationen
»Magnetic Supraparticles as Identifiers in Single-Layer Lithium-Ion Battery Pouch Cells«
S. L. Deuso, S. Ziegler, D. Weber, F. Breuer, D. Haddad, S. Müssig, A. Flegler, G. A. Giffin, K. Mandel, ChemSusChem 2024, e202401142,
»Influence of Phosphate Surface Coating on Performance of Aqueous-Processed NMC811 Cathodes in 3 Ah Lithium-Ion Cells«
Felix Nagler, Nino Christian, Andreas Gronbach, Franziska Stahl, Philip Daubinger, Dr. Andreas Flegler, Dr. Michael Hofmann, Dr. Guinevere A. Giffin
Die Partner
- Carl Padberg Zentrifugenbau GmbH (Projektkoordination)
- Fraunhofer-Institut für Silicatforschung ISC
- Fraunhofer-Institut für Integrierte Schaltungen IIS
- Projektgruppe Magnetresonanz- und Röntgenbildgebung (MRB)
- Friedrich-Alexander-Universität Erlangen-Nürnberg
- Polysecure GmbH
- Pure Devices GmbH
- REELEMENTS GmbH
- iPoint-systems GmbH
- EurA AG
- BASF SE (assoziierter Partner)
- Leclanché (assoziierter Partner)
Letzte Änderung: